tarragona audio
Hi, I am Peter Sikking. I am starting up tarragona audio; an atelier in Berlin where I design and build music‐recording studio equipment.
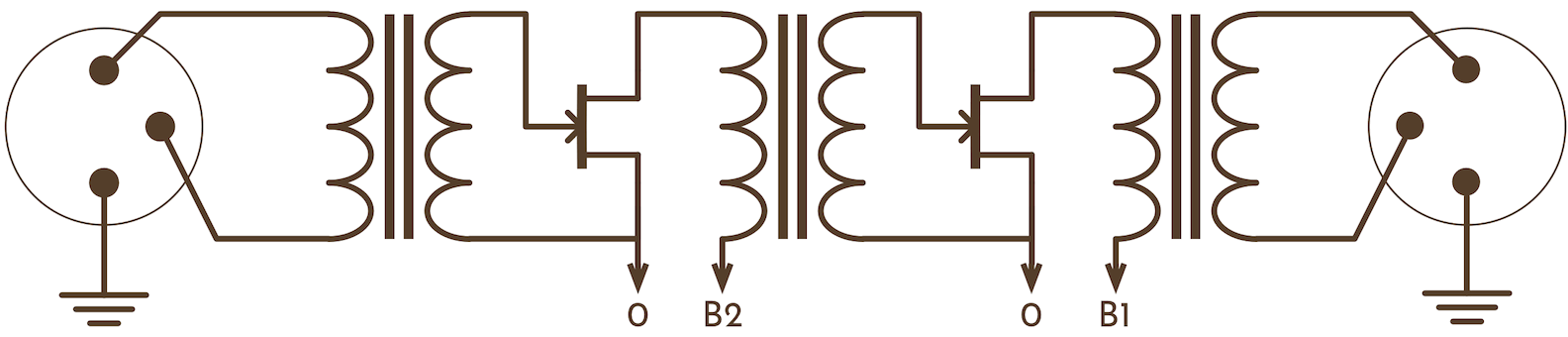
There is a lot of great studio gear on the market today. Most of it can be organised in a few large clusters of products of similar philosophy, design, construction… and at the end, similar sound. Outside these clusters, there is plenty of wide‐open space. There, one can develop new products that tackle the needs of music production in a different way. Or paint a different sonic picture, use unusual circuits, or skip past manufacturing of standard boxes.
I started tarragona audio to do all those four things, out there in free space. With a focus on music—and performance—transport. In particular I do—
- hand‐build to order
Hardware manufacturing—even small boutique runs—comes with a whole set of limitations and dogmas that constrain and limit today’s products. In my designs I explore exactly what manufacturers cannot afford, or bring themselves, to offer. For instance: selecting each individual amplification device and trimming the components surrounding each to further optimise performance.
Non‐manufacturing also allows me to pursue the further points below.
- start free, design methodically, end up outside
the canon
After two decades in interaction design, I now apply its design techniques to studio gear R&D: obtain a deep understanding through user research; take nothing for granted; harmonise product value, user needs and technical possibilities. The result: innovation, because ‘the norm’ has been found to be lacking.
In practice, you can expect fresh thinking regarding principle of operation, functionality, industrial design and ergonomics.
- use circuit designs informed by two decades of building
and designing single‐ended, directly‐heated triode audio
circuits
Discrete, single‐ended circuits with low‐gain, linear amplification devices is how things are done at tarragona audio. But above all, iron—transformers and inductors—is the preferred solution for doing anything—anywhere in my circuits. You can expect lots of iron and not just on the in & outputs.
On the other hand, you won’t see loop feedback, op amps, or printed circuit boards. There are no capacitors anywhere near the signal path, with resistors also frowned upon.
The results is that the energy that underpins the music and performance is conserved at every stage, flowing freely. Call it an un‑mechanical experience; free of ‘that’ sound of electronics.
- offer many customisations for my designs
This starts with features (extras and/or simplifications), settings (dB‐, Hz‐, Ohm‑ranges, number of steps) and enclosures (desktop or rack model; single, dual, or stereo; integrated or external power supply).
reference zone
My designs are right at home in a triangle defined by the following three coordinates:
- 1920–30s movie theatre sound systems, e.g. those produced by Western Electric. Quality was achieved by brute force (feedback did not yet exist), using simple, linear circuits and a lot of transformers and inductors (capacitor tech was in its infancy). The results were spectacular. Today we may sniff at the specs, but in terms of immediacy and transporting the performance, these systems are virtually unrivalled.
- 1950–60s german broadcast (rundfunk) modules; tube models and first‐generation transistor (especially Siemens and TAB). Discrete, single‐ended stages; exquisite, nickel transformers and inductors; brute‐force engineering to get the job done. Today they are legends.
- Vintage, tube, recording and radio broadcast equipment. Boat anchors with just a few big knobs and a large meter.
Note: I do not make copies of any of the historical gear mentioned. My designs start with my own research and a clean sheet; I then apply the attitudes that I associate with these legends in the design process.
coming up
At the moment I am developing the curFET + iron microphone preamplifier. If you find all of this fascinating, why not drop me a line? —ps